作者:徐进 1,2
丁显 1,2
宫永立 1,2何广利 3胡婷 3
单位:1. 中国绿发投资集团有限公司;2. 都城伟业集团有限公司;3. 北京低碳清洁能源研究院新能源技术研究中心
引用: 徐进,丁显,宫永立等.电解水制氢厂站经济性分析[J].储能科学与技术,2022,11(07):2374-2385.
DOI:10.19799/j.cnki.2095-4239.2022.0062
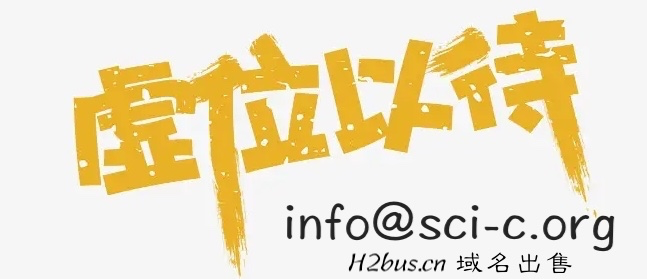
摘 要 氢能是支撑智能电网和可再生能源发电规模化的最佳能源载体,发展电解水制氢是实现碳减排的重要技术路径。当前,电解水制氢成本较高,尚不具备在工业、交通、建筑等领域大规模应用的竞争力。本文对电解水制氢厂站的全生命周期成本进行研究,比较不同技术路线下电解水制氢的成本构成。结果表明,设备购置成本、电力成本和设备耐久性是影响电解水制氢综合成本的关键因素。碱性电解槽由于具有更低的设备购置成本,综合制氢成本低于质子交换膜电解槽。提高电解槽运行温度、开发高效率电解槽以及提高电解槽耐久性可显著降低电解制氢厂站的全生命周期电耗,从而降低制氢综合成本。分析表明,每降低制氢电耗1 kWh/Nm3,可降低氢气平准化成本幅度为1.1 P元/Nm3(P是电价,元/kWh);当电价更低时,氢气的平准化成本也相应降低,电价降低0.01元/kWh,氢气平准化成本的降幅为0.057元/Nm3。
氢能是支撑智能电网和可再生能源发电规模化发展的最佳能源载体,由于具有能量密度高,环保清洁可再生的优势,已成为未来能源发展的重要方向。通过可再生能源电解水制取的氢气,可直接应用于工业、交通、建筑等领域,是实现深度碳减排的有效途径。因此,提高氢能的占比对低碳能源结构的形成至关重要。当前,可再生能源制氢成本仍显著高于化石能源制氢,发展低成本的电解水制氢技术对于推动氢能的快速发展和可再生能源的规模化应用至关重要。目前,电解水制氢技术路线中包括碱性电解水(alkaline electrolysis,AEL)、质子交换膜电解水(proton exchange membrane electrolysis,PEMEL)和固体氧化物电解水(solid oxide electrolysis,SOEL)。其中,SOEL由于运行温度高,能量转换效率高,目前尚未达到商业化应用阶段;AEL和PEMEL技术相对成熟,是目前常用的两类电解水技术路线,但在运行方式和综合制氢成本方面具有较大区别。AEL设备购置成本低,但需要碱液循环,且电解液具有腐蚀性,其运行电流密度低、体积大,因而对电力波动性的响应速度较慢。PEMEL由于使用了更薄的离子导通隔膜和膜电极式的电极构造,运行电流密度显著提高、体积更小,具有快速响应能力,制氢效率也提高。然而,PEMEL采用贵金属为催化剂,设备成本显著提高,与此同时,由于酸性环境下电化学腐蚀问题严峻,电极材料和双极板的耐久性有待验证。在当前的技术经济条件下,无论是采用AEL还是PEMEL,全生命周期制氢成本都是发展规模化制氢的决定性因素。本文采用平准化氢气成本为指标对电解水制氢厂站进行经济性分析,通过全面研究固定投入、设备投入、运维投入的影响因素和影响规律,分析电解水制氢技术指标对经济性的综合影响,并对比AEL和PEMEL技术路线的经济性差异,为低成本电解水制氢技术发展方向提供指导。采用平准化氢气成本(levelized cost of hydrogen,LCOH)作为量化核算电解水制氢经济性的指标,将电解水制氢项目进行全生命周期分析,把所需的固定投入和运维投入折算至每标准立方米氢气,即得到LCOH值,如公式(1)和(2)所示。具体计算公式如下,其中假定电解水制氢运行周期25年,贷款利率按照2021年当前基准利率4.35%。该计算公式做出了以下假设:①电解槽等设备达到设计寿命年限后,残值为零;②每年折旧按照先支出考虑。分析电解水制氢厂站的经济性,覆盖范围包括电力输入至生产出20 MPa氢气整个工艺流程,具体如图1所示。电解水系统在电力和纯水输入的情况下,进行电解制取出压力3 MPa以下的氢气,存储在氢气储罐中,氢气压缩机从氢气储罐抽气,将氢气压力增加至20 MPa,充装于客户的管束车中外售。根据用户特定需求,管束车可将氢气输送到合成氨厂、合成甲醇厂等需求氢气的企业。然而,目前合成氨厂、合成甲醇厂等化工企业,其合成塔中压力需求达20 MPa,因此,本文选用将氢气压力增加至20 MPa于管束车中外售作为主要场景进行分析。根据电解水的技术路线,工艺流程中的电解水系统可以是AEL,也可以是PEMEL;考虑到经济性分析的通用性以及当前电解水系统的技术发展水平,选取当前碱性电解槽达到的单体最大制氢量指标1000 Nm3/h作为电解水系统案例的最小规模单元,其满负荷制氢时的功率需求不超过6 MW,每天的满负荷制氢量折合2 t以上。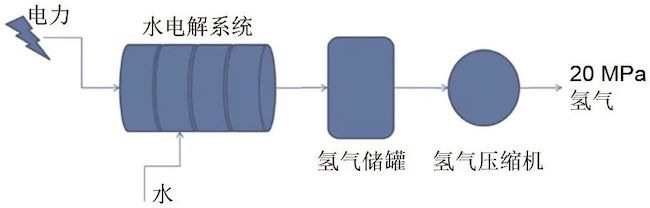
图1 电解水制氢工艺流程示意图制氢站主要用地区域可划分为:① 制氢车间,包括电解槽、制氢电源、充装压缩机和管束车停车位;② 配套设施,包括中控室、办公室、库房等;③ 安全间隙,主要是依据制氢站规范预留安全距离占用的面积。对于典型的制氢站,其用地面积估算为6030 m2,即约9亩,具体组成如表1所示。需要说明的是,制氢设备本身所占用地面积的比例较低,因而,当制氢量变化或采用不同功率密度电解槽时(PEMEL电解槽的功率密度更高,因而设备本身占地面积小),整个制氢站的用地面积不会有显著变化。按照风电场附近征地建设制氢站的场景,一般征地费用约6万/亩,因此,制氢站的土地成本约54万元。可见,当在风电场就地建设制氢场时,土地费用占比较低。制氢厂的建筑工程,除了制氢车间相关部分的基础和防爆围墙等必备的配置外,配套所需的中控室、办公场所和公共设施往往因每个项目的总体使用要求有较大的差异,因此,建筑工程所需的投入应根据设计方案才能提出精确的概算。根据一般工程项目所需的费用,这里假定制氢厂所需的建筑工程投入约为1000万元。对于额定产氢量为1000 Nm3/h的电解水制氢站,其主要设备包括:制氢电源、纯水制取系统、电解槽系统、储罐、压缩机和充装管路系统。按照满负荷制氢综合电耗5.5 kWh/Nm3核算,制氢电源的功率要求为5.5 MW;根据质量守恒,纯水需求量为804 kg/h,因此纯水制取系统的处理能力达到1 m3/h可满足要求;考虑氢气出口压力一般为1.6或者3.2 MPa,则缓存1 h制氢量,需要储罐容积为34.88~69.75 m3,因此选择50 m3容积的氢气储罐可基本满足氢气缓存要求。为达到制氢量的有效充装,需要配置充装压缩机将氢气从1.6~3.2 MPa增压至20 MPa,其有效排量应达到1000 Nm3/h以上,因此选择2台500 Nm3/h的氢气压缩机。其他设备支出包括管路、仪表风系统以及集控系统等,估算合计支出为100万元。当前,电解水制氢比较成熟的技术是碱水和质子交换膜两类。当选择碱水电解槽时,设备购置和安装的总投入估算合计为1900万元,具体如表2所示。分析发现,对于碱水电解制氢厂,电解槽成本占设备投入总成本的50%以上,其次占比较高的是氢气压缩机,约占25%,如图2所示。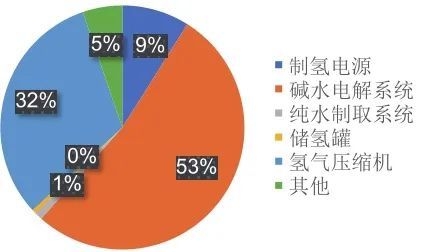
图2 碱水电解制氢设备成本分布当选择PEME制氢时,由于当前没有单体1000 Nm3/h的电解槽,因此需要多个电解槽成组。例如,某公司提供的产品中即包含600 Nm3/h和400 Nm3/h制氢能力的PEMEL,达到1000 Nm3/h制氢量的PEMEL系统购置投入约为7000万元,是同等性能碱水电解系统价格的7倍。制氢厂合计投入设备费用为7900万元,具体如表3所示。其中,PEMEL购置费用占比接近90%,是最大的设备成本投入。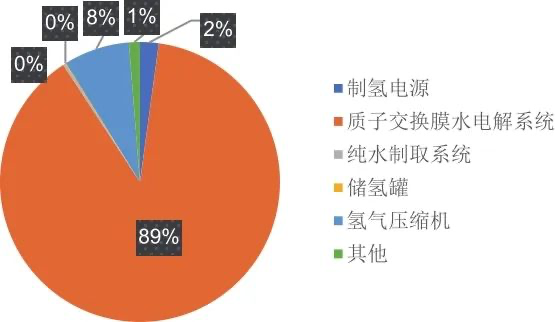
图3 PEMEL电解制氢设备成本分布以上设备投入费用分析结果表明,对于1000 Nm3/h的制氢厂,PEMEL技术路线的设备投入成本显著高于AEL技术路线,达到其4倍。对于制氢能力更高的制氢厂,选用碱水电解设备时的成本优势更为显著,这是由于碱水电解系统的电解槽成本只占总系统成本的一部分,增加制氢规模后,电解槽增加的成本对总系统成本的增加贡献有限;而对于PEMEL系统,其主要成本来自电解槽,因此,更大制氢量下,电解系统成本基本呈线性增加。另一方面,对于制氢量小于1000 Nm3/h的场景,例如,制氢量设计为500 Nm3/h时,AEL系统成本降幅不显著,而PEMEL成本下降显著,此时两个技术路线下的制氢厂设备投入差距会有所减少。初步核算可知,对于500 Nm3/h的制氢厂,采用PEMEL时,总设备投入是采用AEL的3倍。对于AEL和PEMEL制氢设备,设计的使用寿命为20~25年,一般达到预期使用寿命后,电解制氢性能下降至初始性能的80%。制氢厂按照25年进行设备折旧,并假定以当前基准利率4.35%进行核算,AEL和PEMEL两个技术路线下制氢厂每年的设备折旧分别为126.16和524.57万元。制氢厂的电耗主要用于电解槽和压缩机运行。对于AEL和PEMEL,其当前较为先进的综合电耗指标为5 kWh/Nm3 H2。假定制氢厂采用的电解系统初始电耗为5 kWh/Nm3(包含电解槽、冷却、循环水等综合所需电耗),在全生命周期25年服役期间,由于电解槽材料老化导致产氢能力下降,按照线性衰减至初始性能的80%,达到预期寿命时的综合电耗增加为6 kWh/Nm3。根据电解水工厂取电方式,电价将有所区别,具体将在第6部分进行对比分析。对于氢气压缩机,按照50%绝热效率核算压缩电耗,并考虑压缩机冷却电耗占压缩电耗比例为30%,对于制氢厂入口压力1.6 MPa,出口压力平均12.5 MPa(管束车初始压力5 MPa,充装结束压力20 MPa)的操作环境,综合压缩电耗为0.134 kWh/Nm3 H2。将制氢厂的电解和压缩电耗进行整体核算,在25年服役期的电耗指标如表4所示。电解水制氢的水耗与制氢量相关,每制取1 Nm3氢气,理论消耗的纯水量为0.8 L,考虑纯水制取效率80%,则消耗的水量为1 L/Nm3 H2。工业用水价格按照4.1元/m3进行核算。因此,生产每公斤H2的水费为0.04592元。制氢工厂的人员配置包括:厂长、安全管理人员、财会人员和运营人员,其中运营人员按照三班倒、每班3人核算,则制氢厂总计需要12人。按照每人年支出工资8万元核算,共计需要96万元。进行全生命周期核算时,假定人工费根据基准利率增长。制氢厂的维护费用假定按照设备费的固定比例支出,取3%进行核算。这里需要重点说明的是,对于AEL,在其标称的25年服役期间,至少需要经历一次大修,大修成本约占设备成本的20%,当在波动性工况下运行时,电解槽材料发生衰减的速率增加,在服役期间可能需要增加至少1次大修,这将增加额外的设备大修费用。对于PEMEL,目前尚未报道其波动性影响下的寿命影响,但依据燃料电池的变载荷衰减现象,PEMEL在波动性电力输入条件下,预期寿命也会大幅缩短。首先计算制氢厂满负荷制氢的产氢量,按照1000 Nm3/h额定产氢量核算,每年全负荷产氢量为786 t。根据2021年全国的工业用电价格,在低谷期(23:00—次日7:00)和平段期间(7:00—10:00,15:00—18:00,21:00—23:00)内,电价范围基本在0.2~0.5元/kWh。高峰期用电价格基本是低谷期的2倍,则为达到产能全天电价估算为0.5元/kWh。此外电网耦合电解槽具有一定不确定性,产氢量略低于额定产氢量,因此,此处以最大产氢量(额定产氢量)来计算。制氢工厂从电网直接取电进行生产时,根据取电电价可核算出制氢厂生产氢气的平准化成本。取电价为0.5元/kWh,制氢厂按照100%负荷运行,根据设计寿命25年间的总成本支出和产氢总量,对比研究AEL和PEMEL两种技术路线下生产氢气的成本。核算出碱水电解技术路线下的平准化成本为3.15 元/Nm3,各项成本在整个生命周期内的分布如表5所示。结果表明,AEL技术路线下,电费成本约占氢气平准化成本的90%,人工投入成本约占6%,而设备投入成本仅占约4.5%,如图4所示。可见,制氢电耗、电价是影响氢气平准化成本的关键因素,当电价水平在0.5元/kWh左右时,大幅降低电价是提高制氢经济性的决定性措施。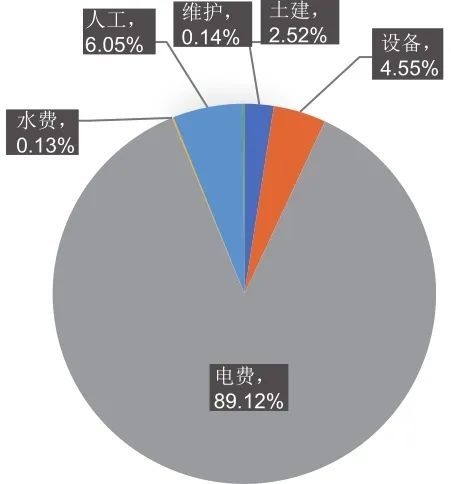
图4 碱水电解各项成本分布核算出PEMEL技术路线下的平准化成本为3.60元/Nm3,各项成本在整个生命周期内的分布如表6所示。结果表明,在当前的设备投入成本下,PEMEL比AEL成本高,若采用PEMEL不能通过提高波动性适应能力从而降低综合制氢电耗,在1000 Nm3/h规模及以上制氢领域,选择PEMEL技术路线的经济性要低于碱水电解。表6 PEMEL技术路线各项成本在整个生命周期内的分布
无论是酸性电解水还是碱性电解水,在全生命周期成本分析计算中,设备成本和电费成本是占主导的。由于酸性电解水高昂的设备成本,PEMEL技术路线的设备成本占比更大(图5)。碱性电解制得氢气平准化成本(3.15元/Nm3)低于酸性电解制得氢气平准化成本(3.60元/ Nm3),因此根据以上可得出结论:在未来氢能发展道路中,酸性电解水在关键材料开发上需要进一步降低成本,随着材料技术跟进其投资回报空间很大,此外两种电解方式中电价对制氢成本均具有关键影响。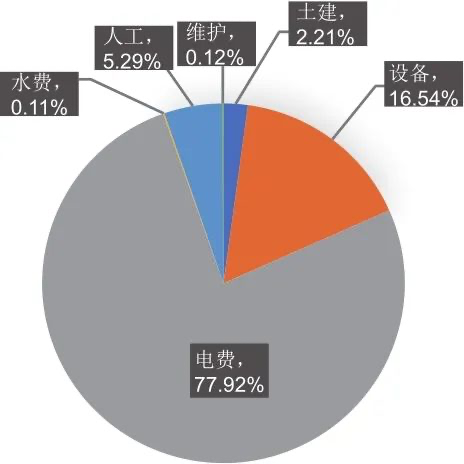
图5 PEMEL电解水各项成本分布考虑碱水电解技术路线下制氢厂,对各电价状态下的制氢平准化成本以及其中电费占比进行分析,计算结果如图6所示。当电价越高时,制氢平准化成本越高,氢气成本(y,元/Nm3)与电价(x,元/kWh)基本满足线性关系y=5.714x+0.339。即使按照电价为0.1元/kWh进行核算,电费占制氢平准化成本的比例仍然高达60%,可见,制氢工厂的总用电费用是影响产氢成本的关键因素。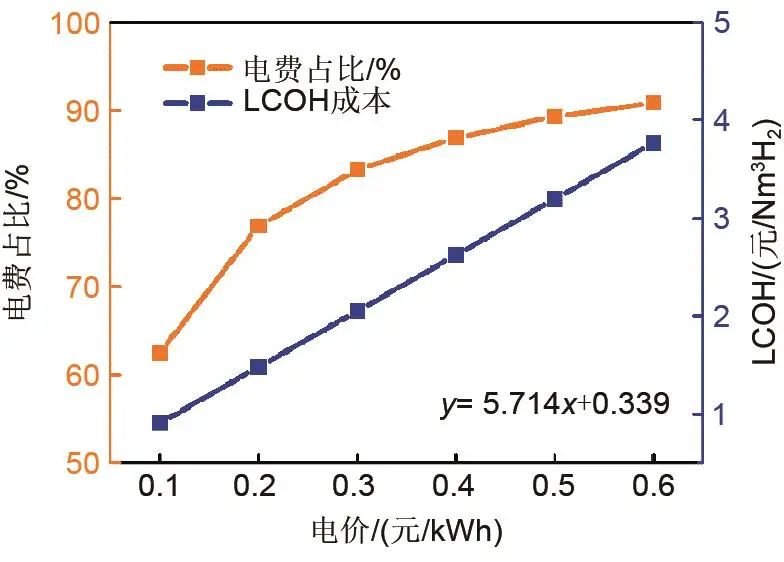
图6 各电价状态下的LCOH以及其中电费占比
制氢工厂总电费成本除了受到电价的影响,也受到电解槽电耗的影响。从全生命周期角度考虑,电解槽电耗与初始性能和预期寿命有关,初始性能越高即电耗越低,电解槽预期寿命越长则说明按照25年服役期限核算时性能下降越平缓、电耗指标增长越缓慢,最终全周期下的电耗也会偏低。AEL和PEMEL的理论电耗可根据电解反应的热力学函数进行计算,通过温度矫正的反应焓变和自由能变化可得到条件标准电压。在25 ℃、0.1 MPa条件下,参与电解水反应的各物质的标准焓和标准熵如表7所示。由于电解水反应一般在80 ℃左右 (AEL运行温度70~90 ℃,PEMEL运行温度50~80 ℃)进行,温度偏离标准状态,因此,需要对反应焓进行温度矫正,采用的函数关系式如下:公式中的T代表的是温度偏离值,幂前参数依据表8进行取值。当获得某温度下的电解水反应焓变后,可进一步根据反应熵变计算出反应自由能变化值。应用法拉第定律,分别采用电解水反应焓变值和自由能变化值,可计算出水电解反应的热平衡电压(thermal-neutral voltage,Utn)和可逆电压(reversible voltage,Urev)。
| 
| (6) |
当假设电解水反应的熵变值恒定情况下,可计算得到各反应温度下的热平衡电压和可逆电压,如表9和图7所示,当输入电压控制在热平衡电压以上时,电解能量效率小于100%,当输入电压控制在热平衡电压之下但处于可逆电压以上时,电解能量效率大于100%,当输入电压小于可逆电压时,电解反应不能发生。当温度在100 ℃以内变化时,热平衡电压基本不变化,相应地,热平衡电解电耗基本维持在3.518 kWh/Nm3H2不变;可逆电解电压则逐渐减小,当温度跨度为30 ℃时,电压变化超过20 mV,温度越高时,理论可逆电解电耗越小。由于电解水反应属于吸热反应(焓变值大于零),热平衡下的理论电耗值始终高于做电功所需的可逆电耗,这导致输入的电能有一部分用来给电解槽产生热量以维持反应温度。按照反应温度80 ℃时核算,这部分电能占能量总输入的比例最高达到20%。因此,如果有可用的低品位热能用于电解槽加热,那么电解实际所需的电耗会显著下降。另一方面,在应对电解槽电力输入的波动性时,由于电解槽热力平衡受到输入电力的影响,尤其是当电解负荷下降但电解槽换热不能及时跟随时,将导致过多的净热量被散出,电解槽平衡热量将消耗更多的电能,导致能耗增加。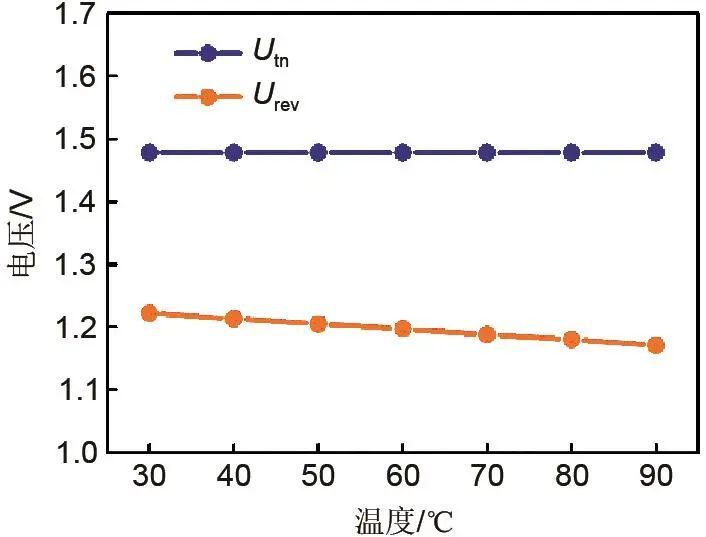
图7 电压随温度的变化规律参考电解水电耗理论值,核算电解水电耗技术水平对制氢工厂LCOH的影响。电耗最低值取理论热平衡下的3.518 kWh/Nm3H2,最高取值参考当前常规电解槽性能水平,假定工作电压为1.85 V,则对应的电耗为4.393 kWh/Nm3H2。当制氢电耗为3.518 kWh/Nm3H2,且按照其25年服役期间性能逐渐下降至初始的80%,假定制氢厂全负荷运行且电价为0.5元/kWh,其他条件均不变,则核算出的制氢厂成本分布如表10所示,LCOH为2.34元/Nm3。当制氢电耗为4.39 kWh/Nm3H2时,其他条件均不变,核算出的制氢厂成本分布如下表11所示,LCOH为2.82元/Nm3。可见,当电耗增加约0.89 kWh/Nm3H2时,制氢成本增加0.48元/Nm3。进一步研究电价为0.5元/kWh下,电解槽电耗与LCOH的关联关系,如图8所示,以电解电耗为横坐标(x,kWh/Nm3H2),LCOH为纵坐标(y,元/Nm3H2),二者近似呈线性关系,电耗每增加1 kWh/Nm3H2时,LCOH增加0.55元/Nm3。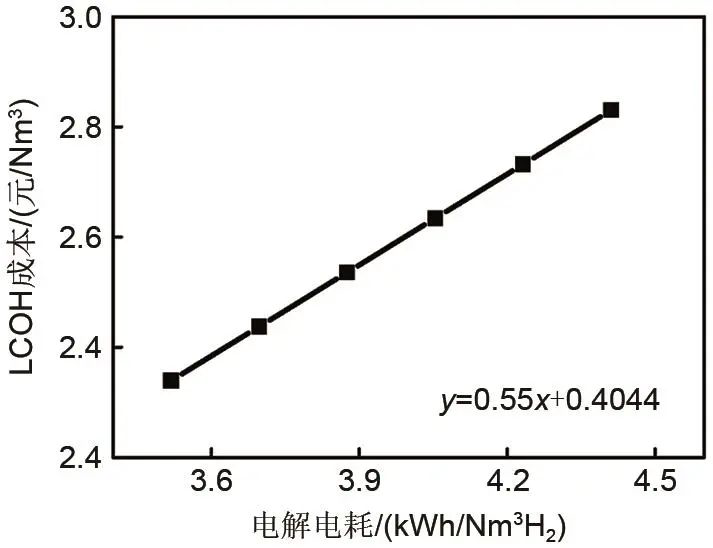
图8 电解槽电耗与LCOH的关联关系继续考虑不同电价下的情况,取最低电价0.1元/kWh,最高电价0.5元/kWh,分析制氢厂LCOH随电解电耗的变化,如图9所示。结果表明,当电价高时,电解电耗对LCOH的影响较为显著,而电价低时,电解电耗对LCOH的影响也随之减弱。例如,当电价为0.5元/kWh时,每增加1 kWh/Nm3H2电耗,LCOH增加0.55元/Nm3,当电价为0.1元/kWh时,每增加1kWh/Nm3H2电耗,LCOH增加值变为0.11元/Nm3。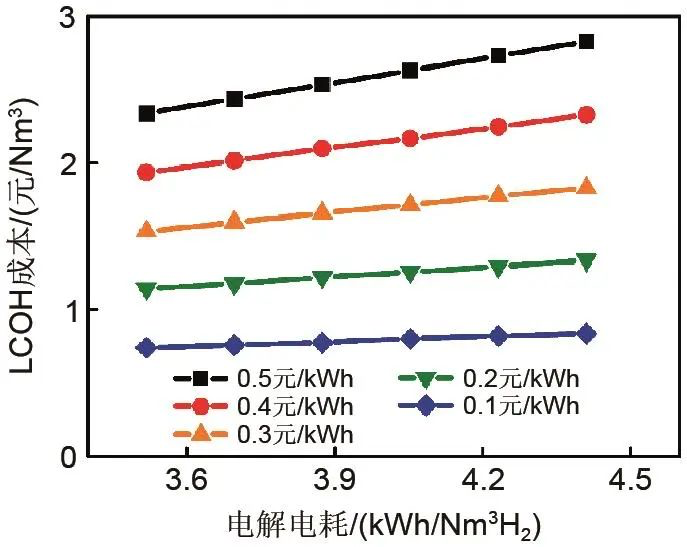
图9 制氢厂LCOH随电解电耗的变化系统地分析电价与制氢成本的影响可知:由于电耗在成本中占比较大,电价基本是决定氢气价格的主要因素,电解槽性能也决定了用电的多少,因此,提高电解槽性能在氢气成本中尤为重要。此外,提高电解槽温度,对降低槽电压、提升电解槽性能十分有益。因此,电解水制氢技术中,研究者们需要在电解水制氢的能量效率和提高电解槽温度等关键技术上重点关注,这意味着:一是在材料层面,PEMEL的质子交换膜需要更加耐高温,AEL在未来发展中使用的阴离子交换膜同样如此。二是在系统层面,在技术上提升电到氢的能源转化效率的同时提升热电的利用效率也同样关键。电解槽寿命影响整个电解系统的全生命周期使用成本,当前大部分电解槽采用的设计是要求在稳定的电源下运行。当电解槽采用波动性电源时,电解槽的运行参数,包括温度、压力、电流密度和电压会发生瞬态变化,这会导致电解槽关键部件发生加速衰减,甚至影响氢气纯度,造成安全隐患,所以电解槽维护成本也是需要考虑的关键点。当前,电解系统作为成套设备,考虑了每年约合设备购置费3%的维护费用,但当电解槽性能发生严重衰减时(例如电解性能降至初始性能的80%或以下时),需要进行大修或更换。对于碱水电解槽,其大修费用约为购置费用的20%,根据实际运行情况,一般需要10年或15年大修一次,这将增加额外的成本支出,核算结果表明,当服役25年期间进行1次和2次大修时,平准化氢气成本将分别增加0.01和0.02元/Nm3,约占总成本的0.1%和0.2%(按照电价0.1元/kWh核算)。可见,对于碱水电解系统,通过大修方法维持其较高的性能,减少电解能耗,是较为经济的选择。假设电解槽在25年间从100%初始性能降低至80%初始性能,则在第12年进行一次大修使得电解槽恢复至初始性能,可以有效降低全生命周期电耗指标,具体对比如表12所示。结果表明,通过大修恢复电解槽性能,可以使得全生命周期的电耗从5.62降至5.37 kWh/Nm3H2,降幅4.5%,即使按照电价为1元/kWh的场景考虑,此时带来的氢气平准化成本降低幅度也达到了2.7%。因此,大修的投入带来的好处是显著的,收益是投入的2倍以上。表12 无大修和1次大修情况下的电解电耗计算 ( kWh/Nm3H2 )
从投运全周期电解耗电成本考虑,电解槽性能稳定是关键的一环。一次大修电解槽恢复至初始性能可减少0.25 kWh/Nm3H2的制氢耗电。由于电费在全生命周期占比中处于主导,所以电解槽的电解性能稳定性是制氢成本进一步下降的关键因素之一。据此可知电解槽耐久性在制氢产业链中是极其重要的。因此,在技术层面,电解水制氢要想产业化应用,如何提高电解水制氢的耐久性是一项十分关键的研究课题,应是研究者们需要关注的重点。电解水制氢经济性主要受到电费成本的影响,降低电价和电解电耗是提高经济性的关键因素。结果表明,采用更低电耗的电解槽将有利于降低氢气平准化成本,每降低1 kWh/Nm3H2电耗,则可降低氢气平准化成本幅度为1.1 P元/Nm3H2(P是电价,元/kWh);当电价更低时,氢气的平准化成本也相应降低,电价降低0.01元/kWh,氢气平准化成本的降幅为0.057元/Nm3。电价基本是决定氢气价格的主要因素,电解槽性能也决定了用电的多少,因此,提高电解槽性能在氢气成本中尤为重要,提高电解水设备温度和能量转化效率在成本控制中十分关键。此外,电解槽的电解耐久性是制氢成本进一步下降的关键因素之一。通过提高电解槽寿命或采取定期维护方式,降低全生命周期电耗,有利于提高制氢厂经济性。第一作者:徐进(1975—),男,硕士研究生,正高级经济师,主要研究方向为绿色能源发展规划与运营管理,E-mail:lvfa_yjy@163.com;
通讯作者:丁显,博士,高级工程师,研究方向为可再生能源与氢能储能技术,E-mail:fd_dingxian@163.com。
相关文章
《储能科学与技术》推荐|郭雨涵 等:基于贪婪算法的分布式储能系统容量优化配置方法
《储能科学与技术》推荐|储能电池系统提供AGC调频的机会成本建模与市场策略
《储能科学与技术》推荐|祝庆伟 等:高能量密度锂离子电池老化半经验模型
平台声明:该文观点仅代表作者本人,氢能网系信息发布平台,我们仅提供信息存储空间服务。
发表评论 取消回复