验证用于评估用于储氢的高压容器中使用的聚乙烯 (PE) 衬里的选定光学方法
>>>小工程师总结:
本文主要对IV气瓶试验中的内胆缺陷进行详细描述,并指出气瓶生产前对内胆监测的重要性以及检测方案。 同时小工程师认为,70Mpa的高压力下,任何的加工缺陷及内胆缺陷都是不应该出现的,只要内胆出现一个薄弱点,那么这个位置必定是应力集中点,这个位置的切应力会很大,千里场地毁于蚁穴就是这个道理。
图 1.高压储氢容器方案。(a)横截面和(b)施工方案:1—进气口凸台,2—复合承载壳体,3—衬里,4—渗透减少溶胶-凝胶涂层,5—圆柱形部分,6—圆顶,内部有可见的PE衬里。
用于压缩气体储存的复合容器由两层组成(图1)。内层(所谓的衬里)负责气体积聚和整体结构的成型。它必须形成足够坚固的屏障,以防止气体颗粒渗透到容器外。衬里可以由金属(合适的钢型或铝合金)或塑料(聚合物)制成。目前,后一种解决方案往往占主导地位。这主要源于现代班轮必须满足的以下要求:
1.储氢系统的最小质量,只能通过使用完全复合的容器(类型4)来确保,其中衬里由聚合物制成,承载外壳由编织碳纤维制成;
2.由于使用了高密度材料和额外的密封性,例如溶胶-凝胶型材料,因此具有最小的氢渗透性[1];
3.由于使用了多年来众所周知的聚合物技术解决方案,例如滚塑、吹塑或挤出,因此易于成型和几何形状修改;
4.对氢气的反应性低,即储存的气体对材料性能的影响很小(例如,消除金属衬里中发生的氢腐蚀问题)。
1.2. 高压复合材料容器中的衬里:材料和制造工艺01
从开发4型高压容器的角度来看,最关键的要素是衬垫。它直接负责气态氢的积累;因此,它的密封性至关重要。根据约束标准,只要不超过 6 Ncm,就允许氢气渗透到容器壁3在容器符合型式认证要求的情况下,每小时氢气、每升容器内部容积 [2] 或存储系统的 <46 mL/h/L 水容量。除此之外,现行法规、规范和标准 (RC&S) 规定,用于制造容器的材料(包括衬垫)必须根据 [4] 表现出所谓的氢相容性。有关氢对聚合物影响的更多信息,请参阅下面的文献研究。同时,衬里在复合层缠绕过程中起到核心的作用,这决定了结构的最终强度。最常见的是,衬垫具有带有非球形几何圆顶的圆柱体形状。衬里还包含金属凸台,可以固定压力阀以及容器和气体装置之间的连接。凸台也可以用作安装把手(在所谓的颈部安装系统中)。衬里可以由金属制成(适当的钢类型或铝合金)。然而,在技术最先进的容器中,衬垫仅由聚合物制成(图 2)。然后,
用于制造衬垫的主要材料是:高密度聚乙烯(HDPE)、聚酰胺(PA6)或PET、聚甲醛(POM)和乙烯乙烯醇共聚物(EVOH)[5,6]。
图2.使用滚塑技术制造的氢气容器的样例性HDPE衬里视图
尽管与整个集装箱相比,班轮的制造成本相对较低,并且在批量生产条件下,但制造高质量班轮的成本不超过10%;需要昂贵的机器园区,以及材料及其加工技术方面的专业知识。通常,通过挤出、滚塑或吹塑成型,或这些技术的某种组合,通过使用塑料接合技术,即挤压圆顶与带有挤压管的集成凸台粘合,生产衬里[7]。金属凸台也可以通过在第二步中直接粘在衬里上来集成在圆顶中[8]。下面给出了两种制造方法的简短描述。衬板生产中最常用的技术之一是滚塑,其中通过同时旋转并将温度提高到约 200 °C 在模具中形成最终产品。 首先,将颗粒形式的金属凸台和聚合物(例如HDPE、PA)放入用于制造衬里的模具中。在此过程中,输入材料沉淀在模具壁上,从而形成衬板的外部几何形状。衬板壁的厚度由放入模具的颗粒量和控制机器运动的程序控制。在冷却阶段,一直持续到模具内部达到环境温度,巨大的压力将新制造的衬板壁推到模具壁上,从而防止收缩过程中的坍塌。冷却过程结束后,成品从模具中取出,只需要对凸台附近的密封面进行质量控制和机械加工。
滚塑的基本优点是衬里上没有连接和焊缝,结构中没有内部张力,可调节壁厚,并且易于形成附加元件(螺纹元件、凸台等)。
滚塑也是多批量生产中最经济的工艺,并且是完全自动化的。
(小工程师点评:注塑、滚塑、吹塑都各自有自己的优缺点,要根据研发现有能力及资源去考虑)一些容器制造商更喜欢使用塑料接头技术制成的衬里,该技术是对管道进行热焊接,形成带有现成圆顶的压力容器的圆柱形部分。这种方法最显着的优点是可以自由选择压力容器的最终尺寸/内部容积,与模具的尺寸无关(滚塑就是这种情况)。011.3. 聚合物衬里——制造和开发相关问题中的最新 (SoA)
专门用于 4 型容器中储氢的聚合物衬里的文献非常广泛,涵盖了大量问题。下面主要选择影响衬里稳定性和透氢性的材料和技术相关问题,并指出:
聚合物老化和热降解
化学结构,包括聚合物链的分子量和分子量分布;
聚合物的结晶度,受其熔融状态的冷却速率的影响
可以诱导影响各种性能的聚合物链的取向和延伸的加工技术)[5,9];
增塑剂、填料、交联剂和其他添加剂的种类和用量,这些添加剂通常用于改变聚合物的性质[;
长期高压氢暴露对聚合物物理性能和力学性能的影响
聚合物的氢渗透率与扩散率和溶解度的关系
渗透速率,这与玻璃化转变温度密切相关;
导致4型高压储氢容器内衬坍塌的参数[;
氢气吸附和随后的氢气容器减压引起的起泡;
材料、容器制造和测试技术(包括衬垫)的标准化 [24];
限制氢气渗透性(例如,通过使用使用溶胶-凝胶技术制成的阻隔层,例如[1,25,26,27]),或使用限制衬里和复合材料之间氢气积聚量的结构(减少所谓的气隙,或在复合材料内部使用通风结构以允许天然氢气逸出);
衬垫耐高温,例如,当高压储氢容器附近发生火灾时[28,29]。另一个目标是所谓的受控缺陷,它允许热通过复合材料壳体传递并导致衬里熔化[9,28]。然后,容器内积聚的氢气通过衬垫中的孔隙泄漏,在这种情况下,孔隙的尺寸会变大,但它会立即在容器表面燃烧,从而确保安全
在 4 型气瓶,主导故障模式与衬垫直接相关。尽管价格低廉,但如果衬垫有故障,它就会消除使用中更昂贵的产品,即整个气瓶。一些衬垫缺陷是由制造技术错误、与所用材料或设计相关的限制以及与整个集装箱相关的开发错误造成的。另一方面,衬里缺陷可能会导致发生现象,例如起泡、屈曲、老化或渗透性增加,稍后与氢气接触。每一种新的4型气瓶结构都首先要经过液压测试:静态和疲劳测试。一系列必要的测试成本很高;然而,从本文作者多年的研究中可以看出,在成品容器,尤其是新容器的液压测试中,通常由于衬垫故障而获得阴性测试结果。以下是作者自己对 4 型氢气高压容器的研究结果检测到的一些衬垫缺陷的精选示例。缺陷通常与以下方面有关:
衬里材料中的气泡和其他夹杂物;衬里几何形状和壁厚不均匀;- 衬里生产过程后聚合物中的残余应力;循环载荷导致的衬里材料裂纹(图3);
- 低于−40°C的低温导致衬里材料出现裂纹(图4);
- 衬板/凸台接头区域的缺陷;
- 金属凸台区域的疲劳裂纹(图 5)。
图3.有缺陷的衬垫的内窥镜图片。(a) 没有可见裂缝的入口穹顶区域和 (b) 凸台-穹顶界面周围有裂缝的出口穹顶区域(用箭头标记)。
图4.在低温循环压力试验后从700 bar氢气容器中提取的具有主要裂纹的PE衬里。(a) 带有进气凸台的切断圆顶和 (b) 没有凸台的衬板,由于衬垫材料界面处的裂缝而脱落。
小工程师点评:除了结构设计问题外,内胆材料低温下的韧性下降是主要原因;01图5.疲劳测试后损坏凸台的视图。(a) 金属凸台出现裂纹,(b) 衬里圆顶内侧出现裂纹。
01小工程师点评:开裂位置为应力集中点,主要是设计缺陷导致
在衬垫缺陷的情况下,构成气瓶承重表面的复合材料通常保持完好无损;NO.1然而,疲劳裂纹发生在衬里中,通常位于圆顶附近或圆顶与圆柱形部分之间的接缝处。凸台和衬里材料之间的连接区域也存在缺陷,或者由材料中的疲劳裂纹引起的凸台缺陷,这种情况不太常见Minor Heat。在新集气瓶结构的开发阶段,缺陷可能是由衬垫本身生产中的技术错误或承重外包装的错误设计引起的。结构复合层中的应力分布不均匀可能导致整个结构中的局部应力集中,进而直接在衬里中引发裂缝。在之前的一项研究中,观察到复合材料结构几何形状的应力分布未优化,因此,在 20–875 bar 压力范围内的环境温度压力循环测试中,衬里开裂(图 6)。
图6.容器模型的 5 度段 (ANSYS V15) 在复合材料中呈现法向应力(纤维取向方向);(a)位于穹顶区域的热点是衬垫损坏和介质泄漏的原因[30]。(b) 在水力试验期间,由于出口圆顶区域的PE衬里出现裂缝(圆顶表面的水滴通过复合材料壳体的孔隙泄漏),氢气容器泄漏的视图。
与不正确的气瓶设计有关的错误,无论是在凸台或衬垫区域,还是在复合材料加固方面,都可以在介绍/鉴定研究阶段(成品气瓶的数值和/或水力测试)进行验证,并且不应在经过认证的气瓶中造成开发问题。在容器的情况下使用批准意味着它们已成功完成了型式批准阶段的整个测试周期;这就是为什么,01只要生产程序是可重复的,在正常生采过程中不应发生与不正确的结构设计相关的缺陷。
另一方面,与衬板生产阶段直接相关的错误在型式批准期间可能无法检测到,并且可能会在集装箱的日常使用中发生。然而,在那个时候,缺陷的后果可能是灾难性的。总而言之,正确制造的衬垫对于高压复合材料容器的整个生产过程具有关键意义。因此,如果开发出一种有效的测试衬垫本身的方法,即在制造后和应用复合涂层之前立即进行测试,则可以显着降低负面后果的成本。应该强调的是,目前的RC&S没有规定制造后应进行的必要衬里测试。在这方面也没有主要来源。
因此,迫切需要开发内衬无损评估(NDE)方法,在生产过程后立即应用,以在早期阶段检测缺陷(例如,气泡和其他夹杂物、内衬几何形状和壁厚缺乏均匀性、聚合物中的残余应力、裂纹以及衬里/凸台接头处的缺陷)。考虑到上述情况,假设这项工作的目标是在产品研发阶段(光纤布拉格光栅 (FBG)、数字图像相关 (DIC))和生产阶段(目视检查)展示所选光学濒死体验方法对衬垫操作评估和分析的适用性。3. 实验方法与数值验证- SUMMER STUDY -使用两种方法对衬垫进行研究:视觉缺陷镜检查和应变场分析。缺陷检查通过目视检查进行,而应变场分析则使用两种互补的方法进行——数字图像相关和基于布拉格光栅的光纤传感。使用有限元法(FEM)进一步验证了应变场测量结果。采用目视检查验证其在制造后对衬板评估的有用性。滚塑工艺生产的衬垫在其结构中可能含有气泡和夹杂物,这会加速压力容器的降解。由于HDPE的半透明性,因此使用目视检查来发现这些类型的缺陷。另一方面,半透明材料比全透明材料更具视觉检查挑战性。
基于光纤光栅(FBG)的数字图像相关和光纤传感等光学方法在高压容器监测中的应用已在许多论文中得到广泛描述[31,32,33,34,35,36]。这些方法分别可用于执行全场和局部位移/应变测量。已经证明,DIC可以有效地作为一种全视场缺陷识别方法,并且可以支持光纤光栅传感器的最佳定位及其校准。光纤光栅传感器需要集成到容器结构中,以便为复合材料高压容器创建嵌入式结构健康监测 (SHM) 系统。在本文中,建议使用这两种方法在实验室条件下(新产品的研发阶段)的压力测试中单独验证衬垫的行为。使用有限元法验证了用互补方法测量的应变场。通过这种方式,对制造和设计方面进行了调查。
013.1. 光纤传感器—光纤布拉格光栅
光纤布拉格光栅是最常用的光纤传感器,用于测量应变和温度变化。由于尺寸小,它们是常见的逐点换能器,也可以很容易地集成到复合材料中(对其结构没有任何负面影响)。单个光栅的长度在5-10 mm范围内,外径约为200-250 μm。由于其出色的多路复用能力,可以将许多FBG组合在一起形成传感器网络[31]。光纤光栅传感器具有在光纤纤芯中形成的特定结构,其特征是折射率值的周期性变化[37]。测量值(变形、温度)与所谓的布拉格波(λB),这取决于光纤尺寸(压缩、拉伸)和热效应(材料的热膨胀和对折射率的热光效应)变化导致的光栅周期(Λ)的变化[38]。013.2. 数字图像相关(DIC)
数字图像相关是一种成熟的位移、应变和形状测量方法[39]。二维DIC(一台数码相机)和三维DIC(两台或更多数码相机)在实验力学领域被广泛应用和接受[40\u201241]。一个简单的测量程序需要获取被调查物体的一组图像,该物体承受任何类型的载荷。选择其中一个图像作为参考图像(在大多数情况下,它是在施加载荷之前获取的图像),其余图像进行相关性分析。参考图像被划分为小的子图像或子集。随后,将子集与在不同加载状态下采集的图像中的相似子集进行匹配。对参考图像的所有子集重复该过程将生成位移图,在以下步骤中,该图可用于计算应变。为了允许应用DIC方法,被研究对象必须在其表面上表现出随机纹理(斑点图案)。在大多数情况下,斑点图案是通过喷涂在油漆上引入物体表面的[31]。023.3. 有限元法
PART.01
目视检查的目的是发现制造过程中引起的任何缺陷(夹杂物、气泡)。由于HDPE是半透明材料,因此使用类似于验光的方法检测材料内部的缺陷。为了找到缺陷,使用了由CMOS相机(CA-H500MX)制成的设置,该相机带有CA-LHE16镜头和环形多光谱光(CA-DRM20X)。对记录的图像进行处理,可以自动检测图像上的缺陷。在图像预处理过程中,使用了对比度校正、亮度和阴影。后来,为了进行缺陷检测,使用了自动功能
PART.02
本研究使用了光纤光栅传感器,即带有Ormocer涂层的“裸光纤”型。它们的特点是没有额外的缓冲涂层,这改善了被监控物体和换能器之间的载荷转移。光纤传感器使用 X60 胶水与物体集成,X60 胶水是一种用于应变片的双组分粘合剂。在安装传感器之前,对表面进行了脱脂处理,并且在局部也去除了用于DIC测量的油漆涂层。传感器沿点安装在布拉格光栅的两端。由于这种方法,沿传感器轴线变形的局部不均匀性与连接点之间的距离一起被平均化。使用解调仪(SI405 HBM)记录信号;它允许以 5 Hz 频率和 1 pm 精度(对应于 2 με 精度)进行测量。®整个衬里总共覆盖着 11 个传感器。传感器的位置如图7所示。表 1 中提供了放置说明。六个传感器放置在衬垫的圆柱形部分(三个在圆周方向上,三个在纵向上)。圆顶上放置了五个传感器(四个同心传感器和一个纵向传感器)。
图7.将传感器放置在衬垫上。(a) 整个衬垫和 (b) 圆顶部分。颜色归因于传感器的不同方向和位置:黑色 - 圆周,红色 - 圆柱形部分的纵向,蓝色 - 圆顶的纵向。
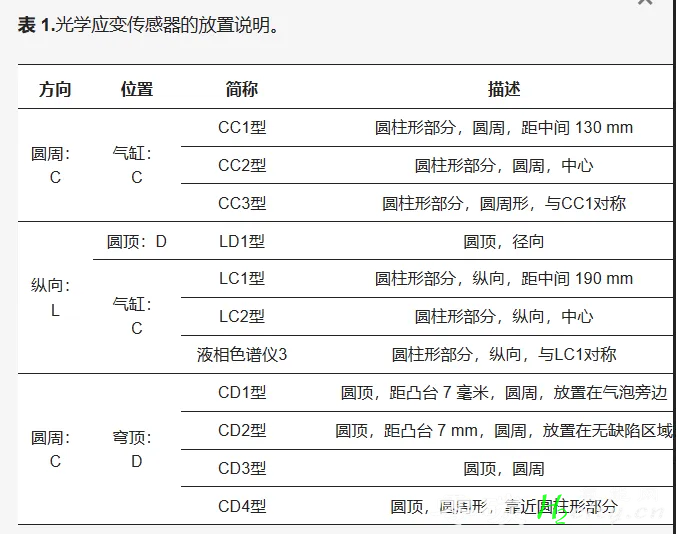
PART.03
4.3. DIC方法
图8.使用DIC方法和光纤光栅传感器进行衬板测试的实验装置。虚线表示使用 DIC 方法检查的衬垫部分。
DIC测量系统的相机安装在三脚架上,距离船只约120厘米。3D DIC系统由两台AVT Stingray 16Mpx相机组成,配备焦距为50 mm的镜头和一台使用Istra4D软件的PC。从单个 3D DIC 测量中获得的一组典型结果参考了笛卡尔坐标系,并包括点云 (x,y,z)、面内位移的两个分量 (U(x,y)、V(x,y)) 和面外位移图 (W(x,y))。应变图是根据“xy”平面中的位移图计算得出的。由于衬垫几何形状的曲率半径很大,并且分析是在衬垫的单侧视图上进行的,因此假设εxx" role="presentation">ε××××××××???应变是沿圆周方向的应变,而εyy" role="presentation">εyy???在纵向(沿生成线)上。这种方法的有效性在[31]中得到证明。为了比较3D DIC测量结果和光纤光栅测量结果,使用了虚拟引伸计。它们位于FBG位置的位移图中。它们的应变计算为传感器连接点之间的平均应变。DIC测试的实验设置如图8所示。在实验过程中,衬里内部装有压缩空气,压力范围为 0 至 1.3 bar。压力增加由压力表和控制阀控制。
024.4. 有限元分析模型
有限元分析模型是在Abaqus/CAE环境下制备的,并使用Abaqus 2020静态线性求解器求解。几何形状是根据测量的测试对象的厚度创建的,并对衬垫的 20 度部分进行建模。在所述分析中,高密度聚乙烯和铝合金被认为是线性弹性材料。凸台和聚合物之间的界面是使用公共节点建立的。模型中使用了 C3D10 命名单元(十节点二次四面体)。在聚合物材料中,圆顶区域(靠近凸台)缺陷被建模为材料中的不连续性,如图 9 所示。使用卡尺在事后测量了沿发电线的壁厚。衬里沿光纤光栅传感器的位置切割(首先沿 LD1-LC-LC3 切割,第二次沿 CC1-CC3 切割)。图 9.有限元分析中使用的衬垫模型,在孔隙率周围缩放网格。
#01
5. 结果与讨论
015.1. 目视检查图 10.带有位于凸台附近的空气链的衬垫入口视图
与压力容器测试相关的经验表明,PART.01
这种缺陷可能导致循环液压加载期间的容器故障(疲劳缺陷、凸台/HDPE接口附近的泄漏)或容器开采过程中的氢气积聚
为了研究该缺陷对凸台周围应变场的影响,将光纤光栅传感器安装在凸台附近(一个靠近缺陷区域,一个靠近无缺陷区域),并对该点进行了有限元分析。
#01
使用光纤光栅传感器获得的测量数据是在从衬垫中抽入和释放空气时记录的。传感器在衬垫表面的位置如表1所示,如图7所示。使用 11 个传感器记录结果。测试期间的变形测量结果如图11所示。
图 11.使用选定的光纤光栅传感器记录变形。(a) 随着时间的推移和 (b) 压力过大。箭头表示压力增加/减少的方向。
在图 11a 中,可以看到加压空气的衬里缓慢加载,在 220 秒后结束。在此之后,空气缓慢释放,直到实验时间的440秒。非恒定压力率是由入口阀的手动控制引起的。在空气释放后,在图11a中,可以观察到衬垫恢复到其初始变形状态的延迟。这意味着其内部压力值恢复了大气压的值,尽管材料的非零变形仍然可见。释放空气后可以观察到长达两分钟的效果。图11b(应变-压力图)显示了机械滞后,这是粘弹性材料(如HDPE)的典型特征。为了显示衬垫的逐点变形状态,表 2 显示了每个传感器在 1 bar 压力下记录的变形值。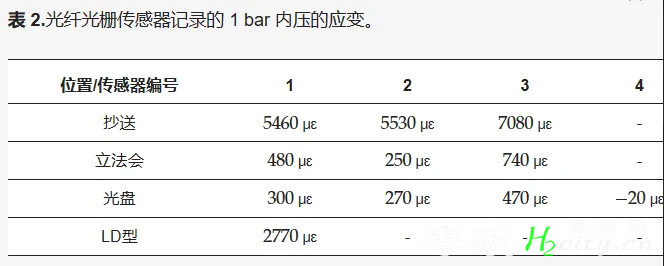
使用DIC方法进行的测量与FBG传感器的测量同时进行,同时将空气泵入衬垫。使用3D-DIC系统分析的变形场包括圆顶的碎片和圆柱形部分的碎片。记录的变形场,在1.0 bar时如图12所示。除了从DIC方法获得的应变场外,还显示了FEM的结果。
图 12.在1-bar压力下圆周和纵向的变形场;(a) DIC 测试结果和 (b) 有限元计算。
圆周方向的应变,(图12a),在最接近衬里中间(所呈现照片的底部)的圆柱体部分具有约7000με的最高值。穹顶的圆周应变明显小(<1000με)。测量显示圆顶区域具有负圆周应变的区域(振幅高达 100 με)。纵向应变(图12b)在圆顶上有最大值(约3500με)。在图 12 中,可以看到三个光纤光栅传感器,可以验证这两种方法。FEM 的结果(图 12 的底部)与两者的 DIC 结果一致和方向。使用有限元分析证实了圆周方向上的压缩观察结果。DIC和FEA沿发电线的衬里变形(如图12所示)如图13所示。
图 13.圆周应变和纵向 使用 DIC 和 FEM 方法沿发电线的方向。负片位置用箭头标记的区域。衬垫的位移显示该位置周围坍塌。
图 13 显示了 DIC 和 FEM 的结果之间的良好相关性和方向。两种方法在圆周方向上都可以看到压缩。这种行为的区域存在于圆顶上,靠近圆柱体。该区域周围的位移变形几乎是圆柱体和凸台最大变形的两倍。这意味着这种行为可以解释为班轮坍塌的存在,这可能是船舶运行过程中的一个弱点。值得注意的是,应变场的可见非均匀性。即使在相同的横截面上,某些区域也显示出不均匀的应变,这归因于厚度变化。连接到衬垫表面的传感器可以放置在发生局部应变非均匀性的区域。因此,传感器测量的平均应变在某些局部点可能会有所不同。这可以解释表2中测量结果的差异。
图 14.沿衬套的气缸部分应变,并带有光纤光栅传感器位置指示
图 15.由靠近凸台的气泡链引起的应变场变化:穹顶区域模型中没有缺陷(a)和椭圆空隙形式的内部缺陷(b)的圆周应变场分布,以及缺陷的位置和几何形状(c)。
035.2.4. FBG、DIC和FEA结果比较
将DIC的结果与使用布拉格光栅记录的变形值进行比较。为了实现这一目标,使用了虚拟引伸计,其位置和方向与光纤光栅传感器的物理位置相同。使用FEM计算的应变进行验证。由于DIC方法的局限性,仅比较了三个传感器的结果。其中一个沿纵向(LD1)放置在圆顶上,两个位于圆柱形部分(CC1—圆周和LC1—纵向)。传感器的位置如图 12 所示。图16显示了使用所有方法记录的变形测量结果的比较。无论测量方向如何,相关性都是可见的。最大的相对误差是衬垫圆柱形部分 (LC1) 的纵向。对于圆柱体部分的圆周方向(CC1),最大相对误差不超过5%。
图 16.使用光纤光栅传感器、DIC方法和有限元分析模型记录的变形图表。
#01
6. 总结
01正确制造的衬里在用于储氢的高压 4 型复合容器的整个生产和开发过程中至关重要。尽管与整艘船相比,班轮的制造成本相对较低,但任何班轮缺陷都可能导致在制造或开发阶段淘汰更昂贵的船舶。因此,开发一种有效的测试衬垫的方法似乎是合理的,即在生产后,甚至在涂覆复合涂层之前。应该注意的是,现行法规、规范和标准 (RC&S) 没有规定制造后的衬板测试方法。在这方面也没有主要来源。本文来源:
Validation of Selected Optical Methods for Assessing Polyethylene (PE) Liners Used in High Pressure Vessels for Hydrogen Storage平台声明:该文观点仅代表作者本人,氢能网系信息发布平台,我们仅提供信息存储空间服务。
发表评论 取消回复